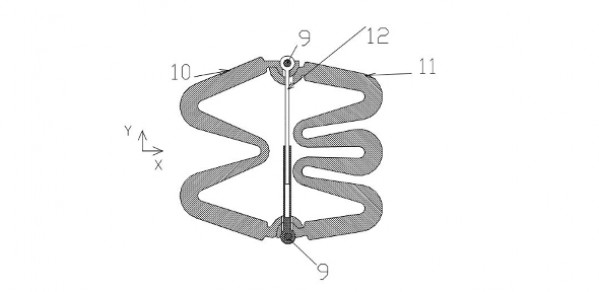
An invention by Salah Elmoselhy, a Postgraduate Researcher here in the Department, is set to shape the next generation of vehicle suspension systems.
Suspension design has traditionally been a compromise between three conflicting requirements: passenger comfort, road holding and load carrying. Vehicle suspension springs absorb road shock by compressing or extending when vehicle wheels encounter bumps and dips in the road. The weight needed to depress a spring a certain amount is called the spring rate. A spring with a low spring rate is soft and can absorb a lot of energy, so generally increases passenger comfort. However, it can decrease road holding and carry only light loads. A heavy, stiff spring with a high spring rate performs well under a heavy load, but can make for a bumpy ride with a light load. A spring rate can be chosen to achieve a compromise, but a better result can be gained if the spring rate of the suspension can be tailored to increase with deflection.
The sections in Salah's E-shaped spring can be designed to produce the required variation in spring rate. Some sections can be profiled to flex easily under light loads and others to provide greater stiffness as the load increases. This can be done without any part of the spring being subjected to undue stresses, which increases the spring's longevity compared with conventional solutions. Two E-springs can be combined in a compact space to create further options for tuning the suspension.
Futhermore, the E-spring is well suited to fabrication using micro-composites in which the glass fibres and the matrix help dampen vibrations and absorb energy. If a damper is needed, because the damping provided by the micro-composite is not sufficient or steel is used instead, then one can be fitted neatly between the springs.
Suspension systems are not just subjected to vertical forces from the wheels on the road; they are also pushed and pulled horizontally by forces created by braking, acceleration and cornering. In conventional systems, struts are used to stabilise suspensions against these forces. The E-spring is inherently more stable than many designs and it is easy to make it completely proof against these horizontal forces by adding a simple C-channel.
The E-spring remedies drawbacks of both of the conventional helical and semi-elliptic multi-leaf springs. The following like-for-like comparisons suggest that the following improvements can be made:
- Weight reduction of 85% leading to reduced fuel consumption
- Space requirement reduction of 75% leaving additional space which could be used, for example, for wider tires, snow chains or storing a spare wheel
- Adjustable spring-rate in the same compact space allowance allowing the suspension system to deal with variable loads and increasing passenger comfort
- Eliminating the cost of a heavy duty hydraulic damper
- Improved fatigue performance.
E-springs can displace both hydraulic dampers and steel springs in both passive and semi-active suspension systems in a reliable, simple, and cost-effective way. Applications span from light pick-up commercial vehicles to heavy trucks and from vehicle suspension systems to tiny mechanical devices such as valves, gears, and actuators embedded in semiconductor chips thanks to the E-spring's inherent scalability.
Salah has received the international honor of being a Laureate of the 2006 SAE Transactions Honor from the Society of Automotive Engineers (SAE), in recognition of his E-springs invention research. The Society of Automotive Engineers is the world premier society for advancing mobility in Land, Sea, Air, and Space.